From Waste to Energy – The technology Inside Amager Bakke
Waste that cannot be recycled is used at Amager Bakke to produce electricity and district heating for homes and companies in the Danish capital.
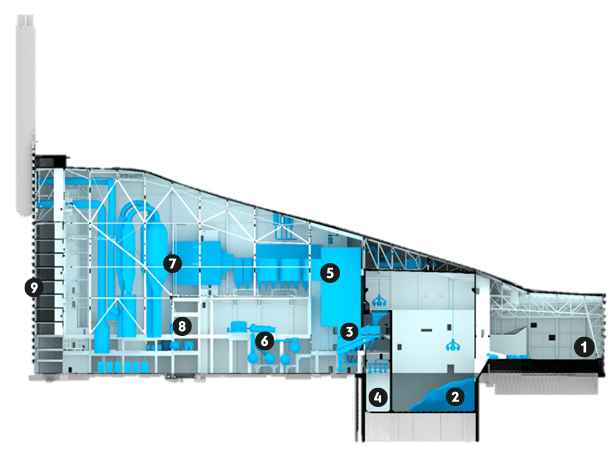
1. Combustible waste arrives
ARC receives combustible waste, and supplies electricity and district heating back to the city.
Amager Bakke only accepts waste that cannot be recycled. This is important, because it’s much better for the environment and climate to recycle things and materials than to use them for energy.
250-300 trucks carrying waste are weighed and registered every day. Around 5% of them are selected for random checks to ensure that the waste is suitable for incineration. We check that the waste they’re carrying is sorted properly, and does not contain anything that can damage the plant, or which are toxic.
2. Waste silo
In the unloading hall, the residual waste is tipped directly into a 30 × 50 metres silo, 36 metres high. The silo can hold approximately 22,000 tonnes of waste. Two automatic grabs mix the waste into a uniform mass. Uniformity is important for the incineration process to be as stable as possible.
Once the waste is mixed, the grabs lift it into the incinerator feed hoppers. Each grab can lift up to 15 tonnes of waste. To reduce obnoxious odours from the waste, the loading hall is kept at a pressure lower than ambient air pressure. The air extracted from the hall is used in the incinerators.
3. Incinerators
Amager Bakke’s two identical incinerator plants each have a capacity of 25-42 tonnes of waste per hour. When the waste is fed into the feed hoppers, it falls down a shaft. It forms an airtight plug here, to maintain negative pressure in the incinerator. The bottom of the incinerator slopes downwards and is composed of 24 rows of perforated steel plates. Each row can move, forming a huge undulating mat, called the grate mat. As the waste moves forward, it gradually ignites. It takes 1.5-2 hours to burn the waste in the incinerator at a temperature of 950-1,100 °C. The temperature is controlled by blowing air through the holes in the grates. When the waste reaches the end of the grate, virtually all of the energy has been released as heated smoke.
For every tonne of waste, Amager Bakke can produce 2.7 MWh of district heating and 0.8 MWh of electricity.
4. Slag and fly ash
When the waste has been incinerated, 17-20% by weight is left as slag. The slag consists of ash from the waste, gravel, sand, metals and other non-combustible materials. The slag is collected in a separate slag silo and transported to a sorting facility. It’s turned and watered for 3-4 months. This process is called maturation. The objective is to cause heavy metal particles to bind to the slag particles so that they cannot be washed out. After maturation, metals are removed for recycling. For every 200 kg of slag, 10-15 kg of metals can be extracted, which can be recycled. The slag is then sieved to give it the same properties as hardcore, and can be used for fill in building and construction projects.
Fly ash extracted from the smoke by the plant’s filters, contains high concentrations of heavy metals and other trace elements. These substances originate from waste that has not been sorted correctly, e.g. batteries. Fly ash and other by-products from smoke purification are used as a substitute for lime to neutralise residues from other industries. The mixture acquires a cement-like hardness and is used to re-create the landscape in a disused limestone quarry.
5. Boilers
Amager Bakke has two boilers, each of which consists of a box with a large number of close-fitting pipes carrying water under high pressure. The incinerators are integrated with their respective boilers, so that the hot smoke from the incinerator rises and transfers its heat energy directly to the water in the pipes. A pump maintains high pressure in the pipes, so that the steam produced has a pressure of 69 bar and a temperature of 440 degrees. Each boiler can produce up to 137 tonnes of steam per hour. The steam from both boilers is collected in a common steam pipe, called a steam rail, and piped to the steam turbine. In order to prevent the incinerators and boilers from expanding when they get hot, they do not stand on the floor, but are suspended from the ceiling by a steel cradle.
90% of the energy from waste is converted to high-pressure steam.
6. Turbines and heat exchangers
A steam turbine consists of a series of impeller blades mounted on a shaft. As the steam expands through the impellers, kinetic energy is generated and the shaft begins to rotate. The shaft is connected to a generator, which converts the energy into electricity. Electricity production is up to 63 MW.
Once the turbine has taken the pressure and heat from the steam, heat energy still remains. That energy is used in the district heating exchangers. District heating water is heated in the exchangers, and then pumped into the district heating network. When the heat in the water has been used by consumers, the water is returned and heated again. District heating production is up to 247 MW.
Amager Bakke can adapt the production of electricity and district heating to the needs of consumers. If a lot of electricity is needed, all of the steam is fed through the turbine. But if a lot of district heating needed, the steam is diverted past the turbine and directly into the heat exchangers. Waste is a resource, which is why ARC adapts production to the needs of the city every single day, all year round. If a lot of energy is needed, the plant converts more waste than when demand is low. In this way, Amager Bakke supports renewable energy from wind and solar energy.
7. Flue gas purification
Once the smoke has passed through the boilers and released its heat, it must be purified. Each incinerator line has a separate smoke purification system, which consists of an electric filter, a catalyst, three scrubbers and a dust filter. Amager Bakke’s smoke purification system is one of the best in the world. Amager Bakke is also the first waste energy plant in Denmark to be equipped with a catalyst to remove nitrogen oxides (NOx).
Most of the dust and ash in the smoke, what we call fly ash, is removed by the electric filter. The smoke is then passed through the catalyst, which removes NOx. The first scrubber removes hydrochloric acid, mercury and other unwanted substances, while the second removes sulphur dioxide using lime. The third scrubber is a ‘condensing scrubber’. Water vapour is condensed into water droplets here, so that heat pumps can utilise residual heat in the smoke. The residual heat is sent through heat exchangers to the district heating network. In total, approximately 20% of district heating production comes from the heat pumps connected to the smoke purification system. The last purification step is a wet dust filter, which removes the last remnants of dust from the smoke.
Before the purified smoke reaches the chimney, it passes a measuring station, which constantly registers the content of pollutants. That means ARC can ensure all environmental requirements are complied with.
8. Water treatment
Waste contains a lot of water, generating a lot of water vapour from incineration. Most of the water is collected by the smoke purification system. At full load in the two incinerators, up to 13 m3 of wastewater is produced per hour. The wastewater begins with a pH value of between 0.5 and 2.5, and is purified and neutralised in four steps:
Firstly, lime and lye are added, which neutralise the wastewater to a pH value of between 7 and 8. In the next step, particles in the water settle as sludge in large tanks. The wet sludge is passed on to a filter press, where most of the water is squeezed out. The sludge is collected in a container and dumped with the fly ash. In step three, the water is passed through sand filters and ammonia strippers. The smaller particles that had not previously settled are then filtered off. The excess ammonia in the ammonia strippers is recycled for flue cleaning. The last cleaning step consists of carbon filters and ion exchange. These remove the last remnants of organic materials and metals.
9. Monitoring
The entire energy plant runs 24/7/365, and the process is monitored around the clock – from weighing in to water treatment. A Control, Regulation and Monitoring System, with approximately 10,000 alarm points and visual systems, allows employees in the control room to monitor the entire process.
Amager Bakke has 850 pumps, blowers and compressors, 1,800 valves and 3,300 measuring instruments.